Gefasoft 開發(fā)了一款體積非常精巧的安全氣囊擴散器光學檢測裝置,它由十一個相機工位組成,每個工位要求不同的檢測時間。Gefasoft 借助高度靈活的 XTS 磁懸浮輸送系統(tǒng)并行運行每一個檢測工位,并能夠提高產(chǎn)品產(chǎn)量。
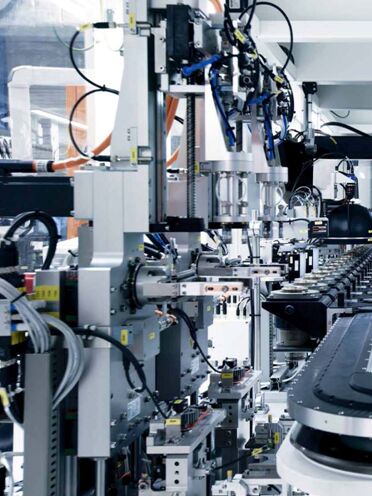
對于復雜的部件形狀,光學檢測系統(tǒng)通常需要用到串聯(lián)或并聯(lián)工位中的一系列相機,以便能夠檢驗所有相關標準。位于雷根斯堡的 Gefasoft Automatisierung und Software 公司的 Sova-VIS 16 系統(tǒng)用于檢測汽車安全氣囊的擴散器。擴散器呈杯狀,由各種形狀的金屬部件拉制而成,直徑約為 60 毫米,是汽車安全氣囊的安全關鍵部件,因此必須詳細檢查擴散器的內(nèi)外表面。

XTS 補償時差并簡化系統(tǒng)擴展 雖然有些檢測任務需要的只是一張圖片,但其它檢測任務需要復雜的照明系統(tǒng)和多個圖像。擴散器內(nèi)壁是特別關鍵的表面,必須對其表面進行仔細檢查,哪怕是尺寸僅為幾十微米的最小缺陷。在零件被精整之前使用線掃描相機可以達到所需的圖片分辨率。僅精整過程就需要約 2 秒鐘的時間,這意味著每個工位的圖像采集時間差別很大。
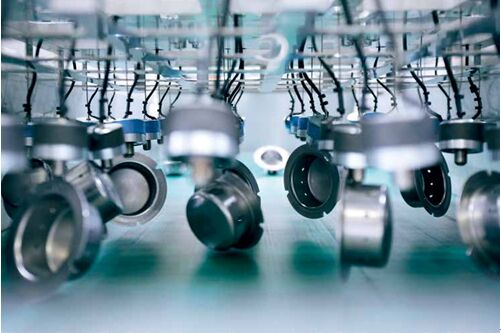
擴散器是安全氣囊和充氣機或氣體發(fā)生器之間的安全關鍵鏈路,必須以最大可靠性快速、有效地對其進行檢查 如果所有相機工位通過如旋轉(zhuǎn)分度臺這樣的剛性系統(tǒng)連接,則圖像采集時間最長的工位將確定整個系統(tǒng)的最短周期時間,且也會相應地限制吞吐率。但是,利用 XTS 解決方案的靈活性,就可以實現(xiàn)以較快速度通過快速檢測工位,給檢測速度較慢的多個工位同時提供檢測組件。Gefasoft 市場部經(jīng)理 Georg Schlaffer 解釋道:“Sova-VIS 16 系統(tǒng)中各個步驟的成像時間各不相同,需要我們找到一個具有靈活的異步傳輸系統(tǒng)的機器布局,這樣,我們就能夠在有限的空間內(nèi)高效地執(zhí)行作業(yè)。倍福的 XTS 系統(tǒng)及其可獨立控制的動子可以完全滿足這些要求。盡管有速度較慢的檢測工位,我們?nèi)阅軌驅(qū)崿F(xiàn) 1.9 秒的平均周期時間。XTS 還讓我們能夠在比同類解決方案小得多的占地面積中實現(xiàn)這一點,以滿足最終客戶的空間需求。
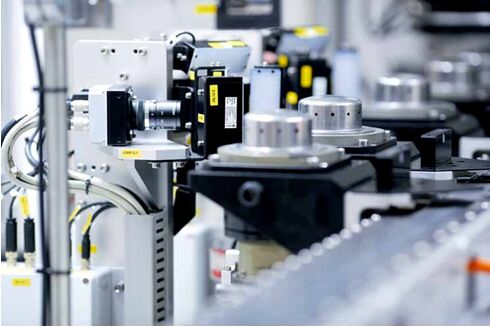
Gefasoft 借助 XTS 磁懸浮輸送系統(tǒng)優(yōu)化了圓柱形金屬部件的質(zhì)量檢查 工程總監(jiān) Christian Schartl 補充說道:“由于對這些部件有高需求,最終客戶規(guī)定的周期小于 2 秒。由于其中兩個檢測步驟花費了近 4 秒鐘的時間,若要實現(xiàn)這一目標就必須重復和并行排列這些工位,而且 XTS 非常靈活,使這一目標實現(xiàn)起來更加容易。其它具有基于輸送帶或輸送鏈的輸送和開關模塊的解決方案會需要更復雜的機械結構,在占用更多的空間的同時速度會更慢! 由于相機檢測工位數(shù)量眾多,XTS 線的總長度達到 11 米,帶有 30 個動子。由于動子重量相對較大,輸送線配備了一個由 Hepco 制造的特殊軌道系統(tǒng)。若要滿足提升和旋轉(zhuǎn)裝置的搬運要求,每個動子的質(zhì)量需要達到約 4 千克(8.8 磅),因為擴散器必須在相機前精確旋轉(zhuǎn)并且能夠移動到兩層(“帽形”和“杯形” )中,以便可以檢查它們的頂部和底部。 一開始的目標是使用單臺檢測機器完全自動化完成之前需要手動完成的過程,包括通過機械手從托盤拾取部件到堆疊或分類這些部件。對于最終客戶來說,通過多臺機器分發(fā)檢測任務并不是一個經(jīng)濟的選擇。除了機器之間復雜的物流及需要更多的空間之外,將擴散器的供給過程與散裝容器分開的成本也太過高昂。Georg Schlaffer 指出 XTS 的另一個重要優(yōu)點:“我們可以借助 XTS 非常靈活地在輸送線上添加更多的加工工位,從而確保系統(tǒng)能夠適應未來需要。” 一個檢測系統(tǒng)即可應對整個過程 在去掉部件表面油污后,它們作為網(wǎng)格托盤中的散裝件被輸送到檢測機器上。夾具從輸送機上取下零件并將它們傳送給 XTS。輸送工位配有一個用來檢測擴散器位置角度及其類型的相機,以確保 XTS 動子的工件夾具能夠正確定向。每個擴散器的頂部壓印了一個批號,它在第一個相機工位中接受檢查。 在檢測到批次號之后,系統(tǒng)會開始檢查擴散器內(nèi)部,這需要在動子中將擴散器從“帽形”旋轉(zhuǎn)到“杯形”位置,即開口向上。為此,要用夾具從動子拾取部件,旋轉(zhuǎn) 180 度后再放回到動子上。同時,撤回內(nèi)部芯棒,使得該部件居中并被放置在其法蘭上。然后在線掃描相機的前面旋轉(zhuǎn),以檢查部件內(nèi)部表面。 Christian Schartl 解釋說道:“事實證明,我們面臨的最大挑戰(zhàn)是空間非常有限,因為相機和四盞燈必須適合內(nèi)徑只有約 60 毫米的部件內(nèi)部。為了解決這個問題,我們必須設計一個集成式照明和相機裝置來深入檢查部件,而伺服電機從外部對接到動子中的可旋轉(zhuǎn)芯棒。此外,必須為照明系統(tǒng)開發(fā)一款高速控制器。將照明裝置移動到部件中并旋轉(zhuǎn)需要的時間超過 2 秒鐘。為了實現(xiàn) 1.9 秒的輸送線周期時間,我們安裝了兩個這樣的檢測工位!
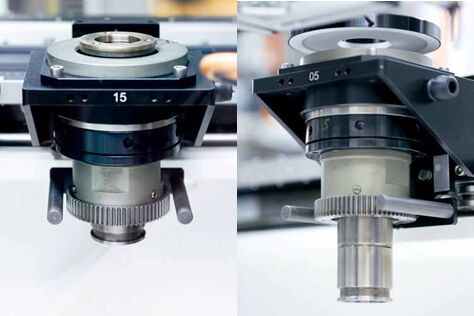
帶有上下芯棒(左圖和右圖)的 XTS 動子沿著“帽形”或“杯形”方向拾取擴散器。還可以看到的是用于在線掃描相機前面旋轉(zhuǎn)部件的鏈輪 緊跟旋轉(zhuǎn)工位后面的是用于檢測材料偏差情況的控制工位和用于檢查擴散器底部的工位。第一個 XTS 直線段的最后一個相機工位負責檢查法蘭是否有質(zhì)量缺陷。這意味著第一個直線段控制六個相機工位。加上完全一樣的線掃描和旋轉(zhuǎn)工位,總共有九個工位。
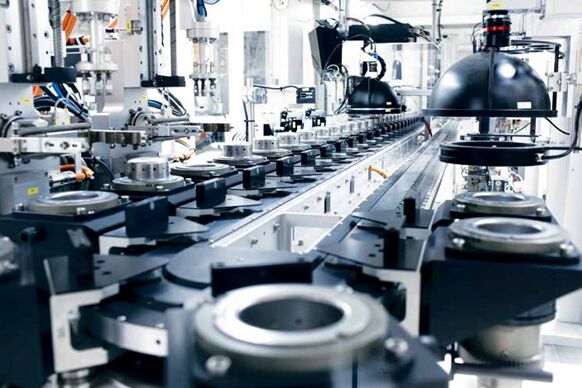
擴散器沿著“帽形”和“杯形”方向運動經(jīng)過檢測工位,其中有些型號完全相同 在動子經(jīng)過 180 度的 XTS 曲線段之后,另一側(cè)有更多的相機工位以及用于標記擴散器的印刷工位。在兩個并行排列的線掃描相機工位檢查部件外表面之前,部件從“杯形”翻轉(zhuǎn)到“帽形”方向。然后是檢測法蘭上部,一臺相機控制式噴墨打印機用于標記與 XTS 動子的運動同步的有缺陷的部件,以及一臺激光器用于標記合格的部件。在第二個 XTS 直線段末端,史陶比爾 TP80 快速拾放機器人從動子拾取部件以等待進一步處理。
|